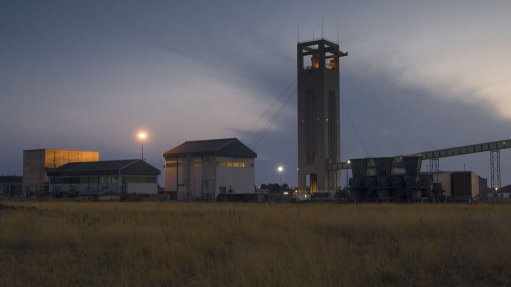
IMPROVING EFFICIENCY
ETA Operations aided Harmony Gold in maintaining previously-implemented electricity cost savings projects that yielded significant results
Photo by: Harmony Gold
JSE-listed Harmony Gold has partnered with Pretoria-based engineering company ETA Operations (ETA), formerly known as HVAC International, to improve the operational efficiency of Harmony’s deep-level gold mines in South Africa, subsequently resulting in significant cost savings.
The operational efficiency improvement project at Harmony’s mines is primarily targeted at areas, such as improving underground conditions, increasing the efficiency of equipment and improving service delivery, says ETA senior consultant Handré Groenewald.
The partnership started in May 2016 and the cost savings as a result of the implementation of new initiatives is approaching the R100-million mark. Further, ETA aided Harmony in maintaining previously-implemented electricity cost savings projects that yielded significant results.
As part of the strategy for the operational efficiency improvement project, ETA developed comprehensive simulations of Harmony’s deep level gold mining operations, with measurements of key operational indicators, such as temperature, relative humidity, and water flow rates, taken throughout the mines.
At some of Harmony’s larger gold mines, the measurement and simulation team spent up to nine months recording various measurements underground, which were used as inputs for simulating various systems such as mine ventilation, cooling, water reticulation and compressed air. The simulations were also combined to simulate the interactive effects of different systems.
The simulations were developed using specialised in-house developed management and simulation systems that apply Industry 4.0 technologies, such as the Internet of Things and Big Data Analytics.
“These systems assist in identifying the root causes of existing operational inefficiencies and finding cost-effective solutions. The systems can also be used to run so-called what-if analyses and predict future operational constraints,” says Groenewald.
The systems further allow for condition monitoring of equipment, with reports or updates on the operational efficiencies.
Apart from the cost savings, achievements from the current operational efficiency improvement efforts include cooler air and water sent underground, increased compressed-air pressures and improved underground ventilation – improvements that have made positive impacts on production.
ETA Operations has also started operational efficiency projects for a platinum miner and a steel producer.
“Our vision is to have data concerning all the important operational elements on a centralised database. From here the data can be analysed, modelled and transformed to valuable information that enables the identification of opportunities to make operations more effective,” ETA Operations senior consultant Jan Vosloo enthuses.
He avers that these technologies and services have proven to increase the bottom line of mining operations and therefore contributes to extending the operational life of mines.